LAB’NOTE
热处理钢铁样品的金相制备
介绍
什么是钢的热处理?钢的热处理是一种可以改变钢的物理性能,某些情况下包括化学性能的热加工工艺。热处理过程包括升温,保温,缓慢或快速冷却等阶段。 这种操作可以改变钢的表面或内部显微组织结构,是用以控制其性能的一种工艺。 钢中添加的合金元素会影响热处理后获得所需组织的效果. 热处理的目的 热处理将增加工件表面甚至芯内部硬度,以提高其耐磨性或抗冲击性。 例如,对于已经经历晶粒扩大的钢,可以使其恢复更均匀的结构。 热处理可以通过消除内应力来提高钢的断裂强度、弹性极限、延展性和降低脆性。 => 因此,目的是根据钢材的最终用途改变其物理性能。
热处理主要工艺
淬火和回火
淬火是将钢的奥氏体转变为马氏体的一种热处理。图1铁碳相图用以确定进行相变处理的温度条件。CCT图(连续冷却转变曲线)则确定了以水、油、气体等将奥氏体转变为马氏体的冷却条件。
Fig. 1: Fe-C diagram
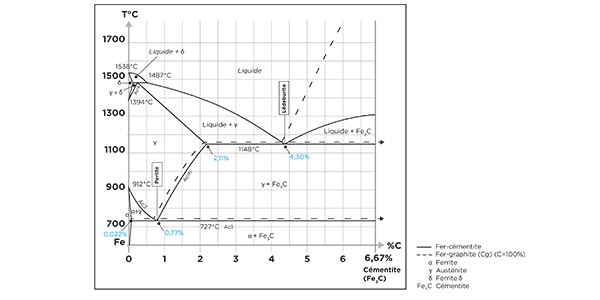
回火是通常在淬火后进行的热处理过程。马氏体硬化后,它是一种应力消除回火,释放材料中存在的应力。回火温度在180至220°C之间。回火不会降低硬度或抗拉强度(或仅略微降低),但会增加延展性和屈服强度。
Fig. 2: Quenching and tempering curve
存在其他类型的回火,可在200至600°C之间进行。通常根据钢的类型及其未来用途进行回火,以获得精确的机械特性。
渗碳处理
渗碳是一种热化学处理,是使渗碳介质中分解出的活性碳原子渗入钢件表层进行扩散的过程。
在实际生产中渗碳的方法较多,根据介质的不同状态可分为固体渗碳、液体渗碳及气体渗碳三种。应用最多的为气体渗碳,它是在具有增碳气氛的气态活性介质中进行的渗碳工艺,通入气体渗剂(来自甲烷、丙烷或丁烷类气体)在高温下分解出活性碳原子,渗入工件表面,以获得高碳表面层的一种渗碳操作工艺。是如今应用最广泛、最成熟的渗碳方法。
渗碳主要应用于低碳钢材料,使其表层富碳至0.6至0.9%,随之通过快速冷却,使富集层硬化。
硬化层深度(CHD)由表面硬度限值为550 HV的垂直距离决定,一般在0.5mm到3mm之间。
主要应用于机械零件,如齿轮、传动轴等。
碳氮共渗
碳氮共渗也是一种热化学处理。介质中碳和氮的结合,可获得比常规渗碳处理更高的表面硬度。
渗氮
渗氮处理是指一种在一定温度下一定介质中使氮原子渗入工件表层的化学热处理工艺,通常是氮原子在500至550°C之间,在合金钢(含铬、铝、钨等)表面的扩散。 氮化处理可形成:
•
化合物层(白亮层):表面的氮化物层,由介质气氛和母材中的化合物组成。 厚度从5 μm到30 μm不等。白亮层具有非常高的耐磨性。硬度一般在950和1100 HV之间。
•
化合物层(白亮层):表面的氮化物层,由介质气氛和母材中的化合物组成。 厚度从5 μm到30 μm不等。白亮层具有非常高的耐磨性。硬度一般在950和1100 HV之间。
扩散层:合金元素的氮化物沉淀为细小的、耐腐蚀的颗粒。这一层的厚度从0.05-0.8毫米不等。它的硬度,取决于母材的不同,可以从400 HV到1200 HV不等。
常见的氮化工艺:盐浴氮化,气体氮化和等离子体氮化。
氮化深度(NHT)是根据遵循DIN 50190-3或ISO 18203标准的硬度曲线确定的。氮化深度对应于心部硬度值加50 HV处所表示的距离。
应用范围:活塞销、曲轴、阀门等
金相制备
无论何种材料,为了展示其最真实的微观组织,需要进行一系列同样重要的金相试样制备步骤,顺序如下: • 从零件中获取待检试样(如有必要),称为“切割”。 • 标准化试样外观尺寸(如有必要),称为“镶嵌”。 • 提升样品表面状态,称为“研磨抛光”。 • 样品表征:(如有必要)利用腐蚀剂腐蚀样品获取微观组织信息,称为“金相腐蚀”;通过光学或电子显微镜观察。 => 这些步骤中的每一步都必须严格执行,否则其之后的步骤将无法展开。

切割
切割的目的是选取试样,以获得一个合适的部分进行检查,而不改变有关材料的物理化学性质。换句话说,必须避免加热或任何可能导致应变硬化的金属变形。切割是零件进一步制备和检验的基础步骤。 PRESI提供自小型精密切割机至中、大型切割设备,以适应不同切割精度、切割尺寸以及切割效率需求:
热处理零件一般具有中大型尺寸。PRESI提供两款设备适用于此类型试样,以满足最苛刻的热处理样品制备需求: •
MECATOME ST310 手动砂轮切割机,功能强大,坚固耐用,完美适用于热处理应用场景。除手动直切模式外,该型号设备具有特殊的摆动切割功能,以减少样品与切割轮的接触面积,加强冷却,最大程度减少损伤层深度,同时极大提高工作效率。
MECATOME ST310 手动砂轮切割机,功能强大,坚固耐用,完美适用于热处理应用场景。除手动直切模式外,该型号设备具有特殊的摆动切割功能,以减少样品与切割轮的接触面积,加强冷却,最大程度减少损伤层深度,同时极大提高工作效率。
•
EVO 400是一台适合于较大尺寸样品的切割机。结构坚固,功率强大,除实验室环境外同时适合于生产环境使用。该设备具有三种工作模式:辅助切割,自动切割,程序切割。并经由彩色液晶触摸屏实现人机交互。 本机还可提供脉冲切割功能,通过交替进给和切割过程中的停顿使得工件内部的应力得以释放。 每一台切割设备都有其配套适用的附件夹具和耗材。夹具与耗材的正确选择对实现良好的切割质量至关重要。 各类附件夹具的重要性显而易见。如果试样在切割过程中未被正确夹持,其将对切割轮,工件,甚至切割设备产生不利影响。
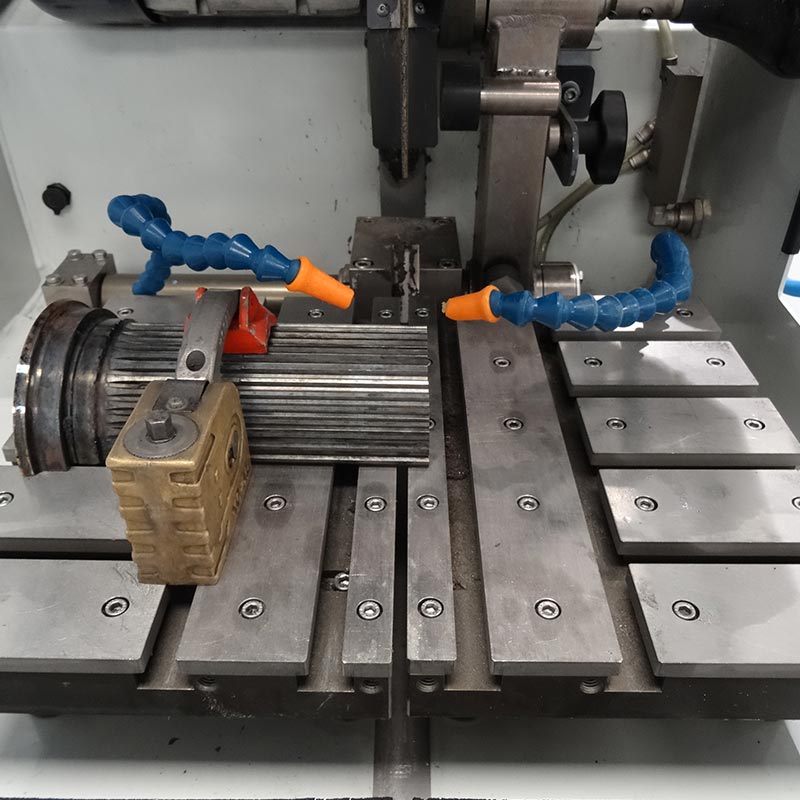
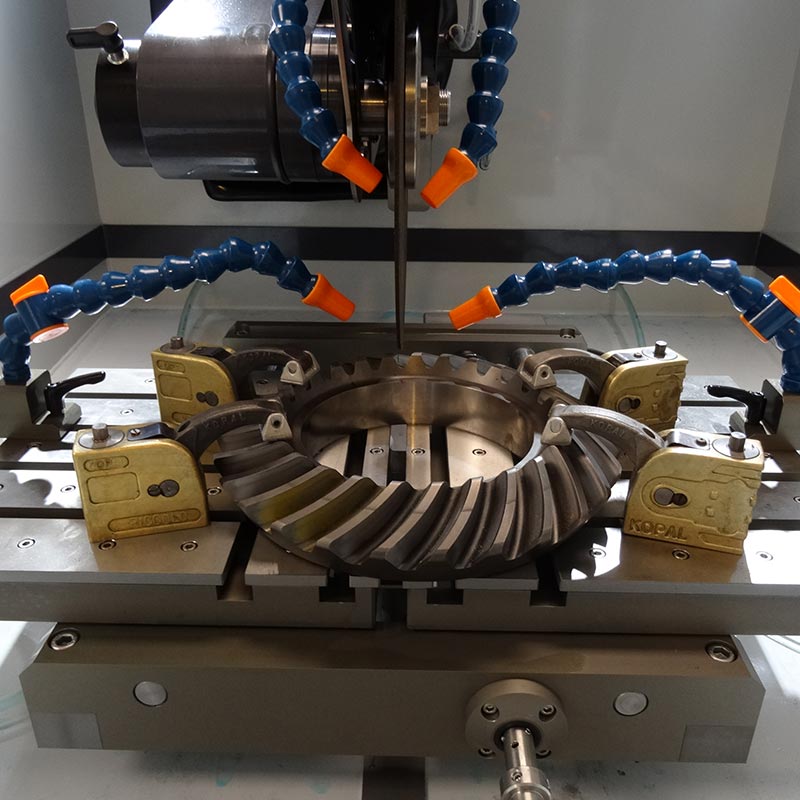
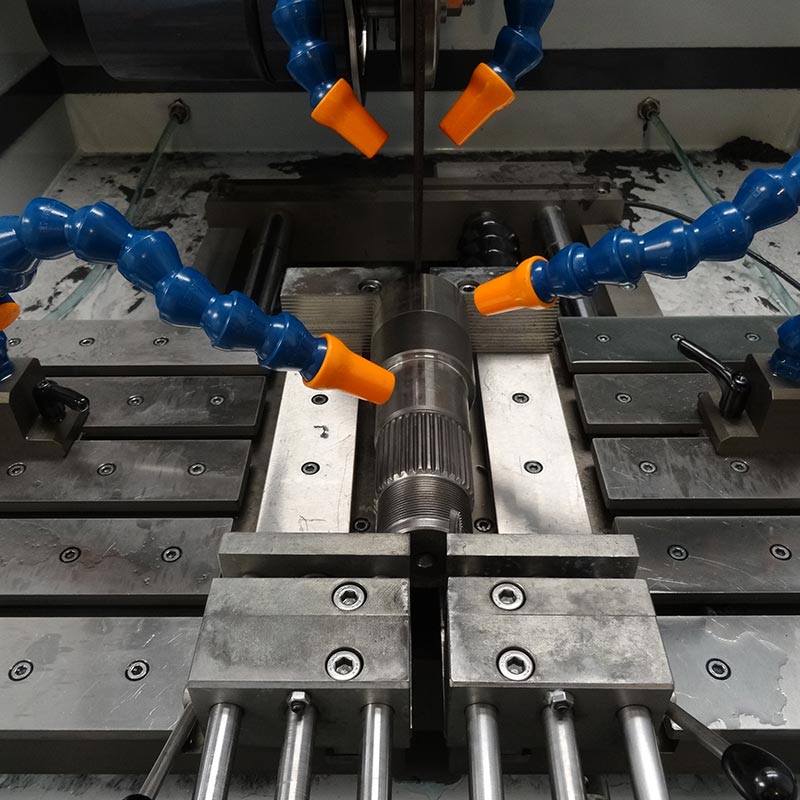
图9到11显示了KOPAL异形夹具和快速虎钳夹具的使用场景。
耗材
所有的切割机都使用由水基和防锈添加剂混合而成的润滑/冷却液,用于改善切割和冷却性能。添加剂还可以保护试样和切割设备免受腐蚀。
![]() |
表面处理钢 | 心部处理钢 |
精密切割 | S Ø180 mm UTW AO | S Ø180 mm CBN |
中型切割 | AO | S CBN |
大型切割 | AO | S |
表1:选择合适的切割轮
=> 适当的切割轮选择,可防止切割失效,或过度的切割轮损耗甚至碎裂。
镶嵌
样品可能因其易碎,尺寸较小,形状各异而不易于手握或夹持。镶嵌,通过统一其外形和尺寸以及包埋保护易碎材料,为后续研磨抛光及进一步分析实验提供帮助。 镶嵌之前,应去除样品毛刺,可能的话,最好以乙醇超声清洗,以确保镶嵌树脂与样品的良好结合,减小树脂收缩。 否则,树脂与样品结合不良以及树脂收缩将引致研磨抛光过程中出现问题。磨料颗粒可能会滞留在试样缝隙中,并在后期游离出来,对样品和抛光表面造成污染和破坏。在这种情况下,建议在每个步骤之间对样品进行超声清洗。 有两种镶嵌方法: •
热镶嵌 i可有效保护样品边缘,或为后续硬度测试需求服务(因其相较于冷镶嵌,能提供更刚性的支撑)。
该方法需经由热镶嵌机实现。
热镶嵌 i可有效保护样品边缘,或为后续硬度测试需求服务(因其相较于冷镶嵌,能提供更刚性的支撑)。
该方法需经由热镶嵌机实现。
PRESI MECAPRESS 3自动热镶嵌机: • 全自动工作循环 • 操作简便:参数设定、储存、调用,保证高可重现性 • 25.4 – 50 毫米,6种内模尺寸
POINT +
热镶嵌在边缘保护、硬度、耐化学腐蚀方面表现出色。
冷镶嵌 更适用于: • 脆性材料,温度/压力敏感材料 • 复杂的几何结构,如蜂窝结构样品 • 需要镶嵌样品数量较大时 Fig 13: 正压镶嵌辅助装置
可使用设备为:
可使用设备为:
+ POINT
大幅提高镶嵌质量,特别是通过减少收缩,优化透明度和促进树脂浸渍。
因为树脂的固化收缩特性,冷镶嵌试样的“背面”易形成不平整表面。在研磨抛光之前,可用砂纸简单打磨使得两端面平行。
耗材
PRESI提供直径20-50毫米的、不同材质的多种模杯,包括KM2.0“一次性”模杯,特氟龙、橡胶、聚乙烯模杯等。为应对不同使用需求,也可提供不同尺寸的长方形模具。

研磨抛光
研磨抛光是试样制备的最后一个步骤。在每一个步骤中,均使用比之前一个步骤更细小的磨削颗粒来磨制样品表面,以最终得到一个高度平整的样品表面,消除残留的划痕和缺陷,以免影响微观分析、硬度测试、显微组织观察等实验目的。PRESI提供一系列手动与自动研磨抛光设备,包含丰富的夹具、附件等配件,以满足从预磨直至最终抛光、单个或批次样品的工作需求。 其中MECATECH系列自动磨抛机更适合于硬度测试类应用要求。
耗材及磨抛工艺步骤
下述所有磨抛工艺步骤均为常用的推荐信息,可根据实际工况灵活调整。
每种工艺的第一步都被称为“求平”步骤,即快速去除材料(及镶嵌树脂)表面,使其平整。
施加于样品的压力将由其面积尺寸决定。通常而言,在粗磨步骤中,每10毫米直径样品可施加1daN(10牛顿)力,即Ø40mm=4daN,并在之后的每个抛光步骤中逐步递减0.5daN.
下述磨抛工艺适用于表面及心部热处理钢的制备
:
使用I-Max R 54 μm金刚石磨盘已足够实现对经金相切割后的样品进行粗磨。如果粗磨步骤需要去除更多的材料,则应使用较大磨削颗粒尺寸(75μm甚至125μm)的I-Max R磨盘。
I-Max R树脂基金刚石磨盘可替代传统的数百张砂纸。它们在粗磨较硬的铁基材料时提供了良好的平整度。
粗磨时,不必要使工作头与磨盘反向旋转,以免影响样品表面平整度。然而,当需要进行大量的材料去除时,设定两者反向旋转将有所帮助。
完成前三个步骤已足够满足硬度测试需求。3μm悬浮液所形成的划痕将不至影响对硬度压痕的测量。RAM抛光布也可以ADR II抛光布替代。
若需进行显微结构及组织观察,可以NT抛光布配合1μm金刚石悬浮液进行精抛。
最后,以PRESI n°3氧化铝悬浮液进行氧化物抛光,可用于夹杂物检测场景。
以下是另一种适用于表面及心部热处理钢的制备磨抛工艺:
步骤 | 磨抛介质 | 悬浮液/润滑液 | 底盘转速(RPM) | 工作头转速(RPM) | 旋转方向-底盘/工作头 | 时间 |
1 | I-Max R 54μm | Ø / 水 | 300 | 150 | ![]() ![]() |
3’ |
2 | MED-R | 9μm super abrasive / Ø | 150 | 135 | ![]() ![]() |
4’ |
3 | RAM | 3μm LDP / Reflex Lub | 150 | 135 | ![]() ![]() |
3’ |
4 | NT | 1μm LDP / Reflex Lub | 150 | 135 | ![]() ![]() |
1’ |
5 | NT | Al2O3 n°3 / 水 | 150 | 100 | ![]() ![]() |
1’ |
在这个方法的第二道步骤使用了MED-R磨盘。这种磨盘合成了多孔树脂垫,并与一种专用的二合一超级磨削颗粒悬浮液配合使用,可代替若干道粗磨步骤,并同时保持良好的样品平整度。
步骤三和步骤四金刚石抛光步骤中使用了LDP多晶金刚石悬浮液。其中的多晶金刚石颗粒具有更多的锋利尖角,适合于对中硬到高硬材料的抛光。
如果工作对象材料对腐蚀敏感,可以用醇基、无水多晶ADS金刚石悬浮液代替LDP多晶金刚石悬浮液。
有时需要根据热处理工艺,尤其是经渗氮处理的样品,来调整磨抛工艺。
步骤 | 磨抛介质 | 悬浮液/润滑 | 底盘转速(RPM) | 工作头转速(RPM) | 旋转方向-底盘/工作头 | 时间 |
1 | Sic P320 | Ø / 水r | 300 | 150 | ![]() ![]() |
1’ |
2 | TOP | 9μm LDP / Reflex Lub | 150 | 135 | ![]() ![]() |
4’ |
3 | RAM | 3μm LDP / Reflex Lub | 150 | 135 | ![]() ![]() |
3’ |
4 | NT | 1μm LDP / Reflex Lub | 150 | 135 | ![]() ![]() |
1’ |
5 | NT | Al2O3 n°3 / 水 | 150 | 100 | ![]() ![]() |
1’ |
使用P320砂纸已足够实现对经金相切割后的样品进行粗磨。如果粗磨步骤需要去除更多的材料,则应使用较大磨削颗粒尺寸的砂纸。
I-Max R或MED-R磨盘,因其相较于碳化硅砂纸更高效的材料去除能力,有可能损伤白亮层,由此建议以碳化硅砂纸取而代之。
之后,以一系列抛光布及不同粒度LDP多晶金刚石悬浮液(辅之以Reflex LUB抛光润滑液)展开研磨抛光。最后,可以氧化铝悬浮液与NT抛光布组合做最终的氧化物抛光。

硬度测试
通常,以进行硬度测试来检查热处理零件的一致性。即,局部热处理时从表层到心部的硬度变化;以及在整体硬化,工件整体的硬度变化。HZ 10-4硬度计以辅之PRESI Touch Pattern硬度软件即可实现该实验目的。
图28:HZ 10-4显微硬度计
图31:感应淬火样品测试结果图表